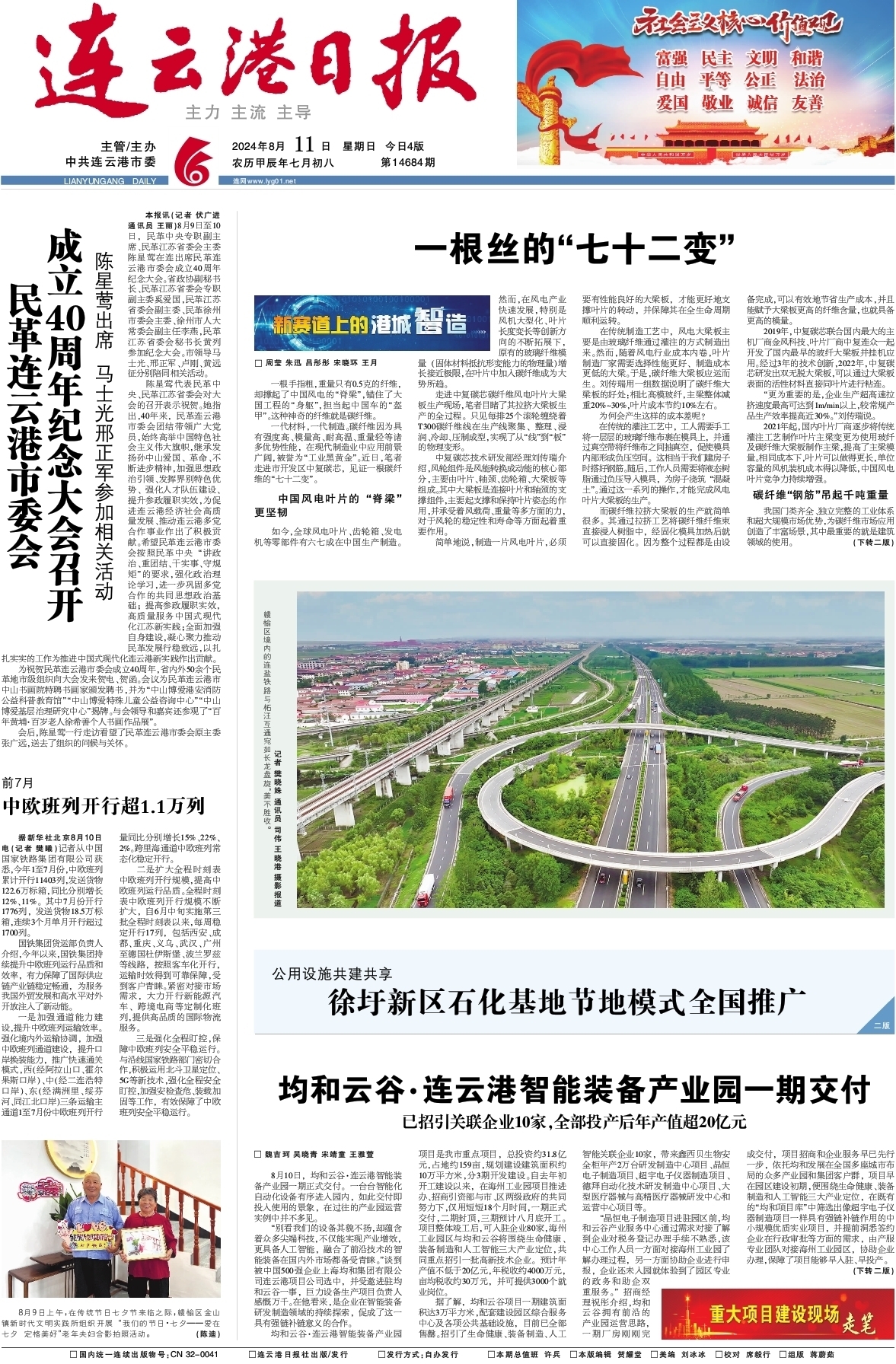
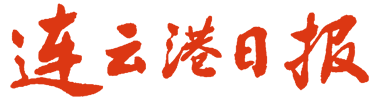
一根丝的“七十二变”
□ 周莹 朱迅 吕彤彤 宋晓环 王月
一根手指粗,重量只有0.5克的纤维,却撑起了中国风电的“脊梁”,锚住了大国工程的“身躯”,担当起中国车的“盔甲”。这种神奇的纤维就是碳纤维。
一代材料,一代制造。碳纤维因为具有强度高、模量高、耐高温、重量轻等诸多优势性能,在现代制造业中应用前景广阔,被誉为“工业黑黄金”。近日,笔者走进市开发区中复碳芯,见证一根碳纤维的“七十二变”。
中国风电叶片的“脊梁”更坚韧
如今,全球风电叶片、齿轮箱、发电机等零部件有六七成在中国生产制造。然而,在风电产业快速发展,特别是风机大型化、叶片长度变长等创新方向的不断拓展下,原有的玻璃纤维模量(固体材料抵抗形变能力的物理量)增长接近极限,在叶片中加入碳纤维成为大势所趋。
走进中复碳芯碳纤维风电叶片大梁板生产现场,笔者目睹了其拉挤大梁板生产的全过程。只见每排25个滚轮缠绕着T300碳纤维线在生产线聚集、整理、浸润、冷却、压制成型,实现了从“线”到“板”的物理变形。
中复碳芯技术研发部经理刘传瑞介绍,风轮组件是风能转换成动能的核心部分,主要由叶片、轴颈、齿轮箱、大梁板等组成。其中大梁板是连接叶片和轴颈的支撑组件,主要起支撑和保持叶片姿态的作用,并承受着风载荷、重量等多方面的力,对于风轮的稳定性和寿命等方面起着重要作用。
简单地说,制造一片风电叶片,必须要有性能良好的大梁板,才能更好地支撑叶片的转动,并保障其在全生命周期顺利运转。
在传统制造工艺中,风电大梁板主要是由玻璃纤维通过灌注的方式制造出来。然而,随着风电行业成本内卷,叶片制造厂家需要选择性能更好、制造成本更低的大梁。于是,碳纤维大梁板应运而生。刘传瑞用一组数据说明了碳纤维大梁板的好处:相比高模玻纤,主梁整体减重20%~30%,叶片成本节约10%左右。
为何会产生这样的成本差呢?
在传统的灌注工艺中,工人需要手工将一层层的玻璃纤维布裹在模具上,并通过真空带将纤维布之间抽真空,促使模具内部形成负压空间。这相当于我们建房子时搭好钢筋。随后,工作人员需要将液态树脂通过负压导入模具,为房子浇筑“混凝土”。通过这一系列的操作,才能完成风电叶片大梁板的生产。
而碳纤维拉挤大梁板的生产就简单很多。其通过拉挤工艺将碳纤维纤维束直接浸入树脂中,经固化模具加热后就可以直接固化。因为整个过程都是由设备完成,可以有效地节省生产成本,并且能赋予大梁板更高的纤维含量,也就具备更高的模量。
2019年,中复碳芯联合国内最大的主机厂商金风科技、叶片厂商中复连众一起开发了国内最早的玻纤大梁板并挂机应用。经过3年的技术创新,2022年,中复碳芯研发出双无脱大梁板,可以通过大梁板表面的活性材料直接同叶片进行粘连。
“更为重要的是,企业生产超高速拉挤速度最高可达到1m/min以上,较常规产品生产效率提高近30%。”刘传瑞说。
2021年起,国内叶片厂商逐步将传统灌注工艺制作叶片主梁变更为使用玻纤及碳纤维大梁板制作主梁,提高了主梁模量。相同成本下,叶片可以做得更长,单位容量的风机装机成本得以降低,中国风电叶片竞争力持续增强。
碳纤维“钢筋”吊起千吨重量
我国门类齐全、独立完整的工业体系和超大规模市场优势,为碳纤维市场应用创造了丰富场景,其中最重要的就是建筑领域的使用。(下转二版)
江苏路特数字科技有限公司 仅提供技术服务支持, 文字、图片、视频版权归属发布媒体