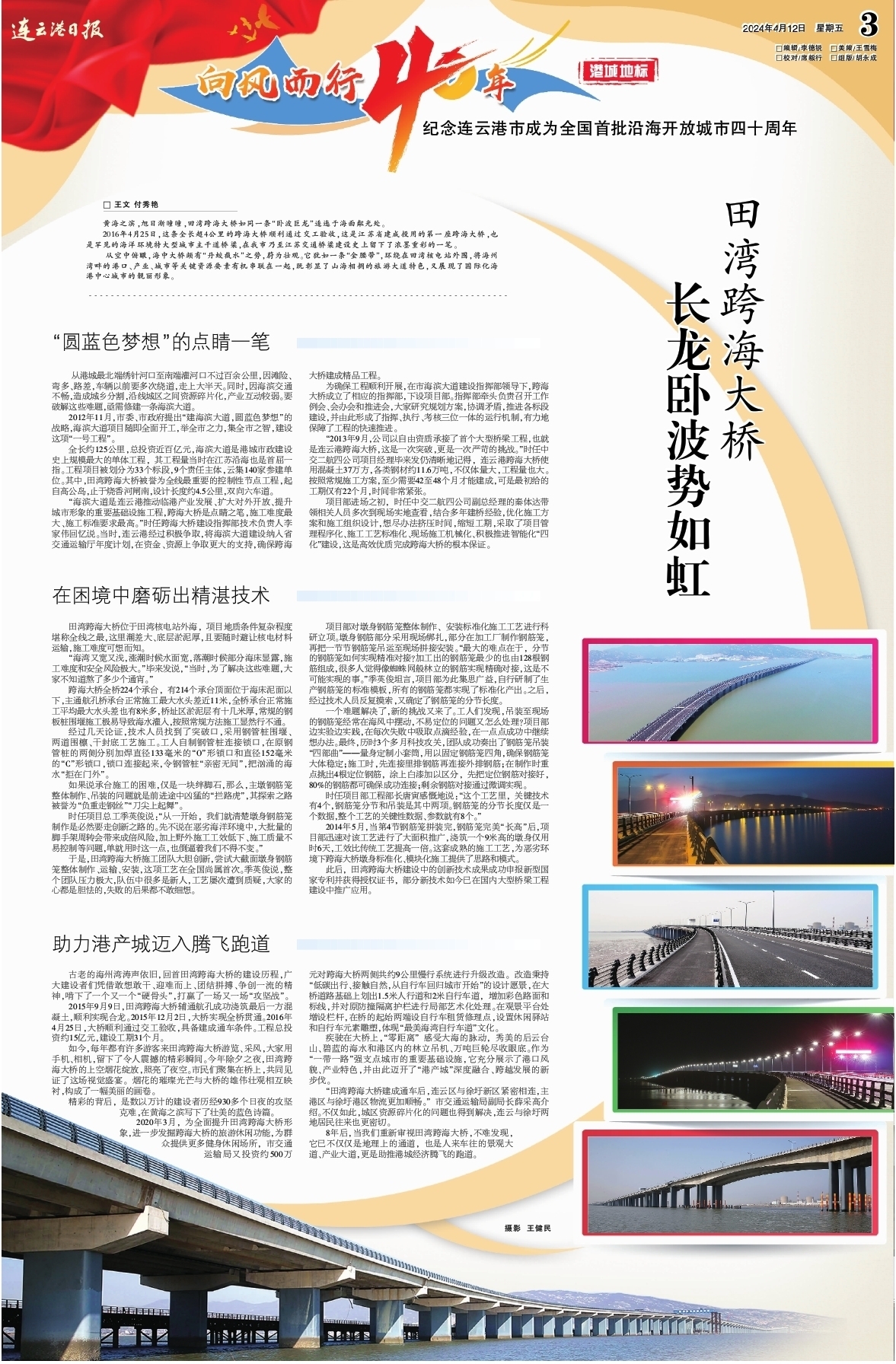
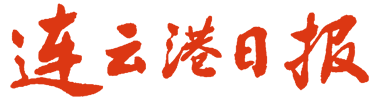
在困境中磨砺出精湛技术
田湾跨海大桥位于田湾核电站外海,项目地质条件复杂程度堪称全线之最,这里潮差大、底层淤泥厚,且要随时避让核电材料运输,施工难度可想而知。
“海湾又宽又浅,涨潮时候水面宽,落潮时候部分海床显露,施工难度和安全风险极大。”毕来发说,“当时,为了解决这些难题,大家不知道熬了多少个通宵。”
跨海大桥全桥224个承台,有214个承台顶面位于海床泥面以下,主通航孔桥承台正常施工最大水头差近11米,全桥承台正常施工平均最大水头差也有8米多,桥址区淤泥层有十几米厚,常规的钢板桩围堰施工极易导致海水灌入,按照常规方法施工显然行不通。
经过几天论证,技术人员找到了突破口,采用钢管桩围堰、两道围檩、干封底工艺施工。工人自制钢管桩连接锁口,在原钢管桩的两侧分别加焊直径133毫米的“O”形锁口和直径152毫米的“C”形锁口,锁口连接起来,令钢管桩“亲密无间”,把汹涌的海水“拒在门外”。
如果说承台施工的困难,仅是一块绊脚石,那么,主墩钢筋笼整体制作、吊装的问题就是前进途中凶猛的“拦路虎”,其探索之路被誉为“负重走钢丝”“刀尖上起舞”。
时任项目总工季英俊说:“从一开始,我们就清楚墩身钢筋笼制作是必然要走创新之路的。先不说在恶劣海洋环境中,大批量的脚手架周转会带来成倍风险,加上野外施工工效低下、施工质量不易控制等问题,单就用时这一点,也倒逼着我们不得不变。”
于是,田湾跨海大桥施工团队大胆创新,尝试大截面墩身钢筋笼整体制作、运输、安装,这项工艺在全国尚属首次。季英俊说,整个团队压力极大,队伍中很多是新人,工艺屡次遭到质疑,大家的心都是胆怯的,失败的后果都不敢细想。
项目部对墩身钢筋笼整体制作、安装标准化施工工艺进行科研立项。墩身钢筋部分采用现场绑扎,部分在加工厂制作钢筋笼,再把一节节钢筋笼吊运至现场拼接安装。“最大的难点在于,分节的钢筋笼如何实现精准对接?加工出的钢筋笼最少的也由128根钢筋组成,很多人觉得像蜘蛛网般林立的钢筋实现精确对接,这是不可能实现的事。”季英俊坦言,项目部为此集思广益,自行研制了生产钢筋笼的标准模板,所有的钢筋笼都实现了标准化产出。之后,经过技术人员反复摸索,又确定了钢筋笼的分节长度。
一个难题解决了,新的挑战又来了。工人们发现,吊装至现场的钢筋笼经常在海风中摆动,不易定位的问题又怎么处理?项目部边实验边实践,在每次失败中吸取点滴经验,在一点点成功中继续想办法。最终,历时3个多月科技攻关,团队成功奏出了钢筋笼吊装“四部曲”——量身定制小套筒,用以固定钢筋笼四角,确保钢筋笼大体稳定;施工时,先连接里排钢筋再连接外排钢筋;在制作时重点挑出4根定位钢筋,涂上白漆加以区分,先把定位钢筋对接好,80%的钢筋都可确保成功连接;剩余钢筋对接通过微调实现。
时任项目部工程部长唐寅感慨地说:“这个工艺里,关键技术有4个,钢筋笼分节和吊装是其中两项。钢筋笼的分节长度仅是一个数据,整个工艺的关键性数据、参数就有8个。”
2014年5月,当第4节钢筋笼拼装完,钢筋笼完美“长高”后,项目部迅速对该工艺进行了大面积推广,浇筑一个9米高的墩身仅用时6天,工效比传统工艺提高一倍。这套成熟的施工工艺,为恶劣环境下跨海大桥墩身标准化、模块化施工提供了思路和模式。
此后,田湾跨海大桥建设中的创新技术成果成功申报新型国家专利并获得授权证书,部分新技术如今已在国内大型桥梁工程建设中推广应用。